Aramid Fabric was made by Aramid Fibers.
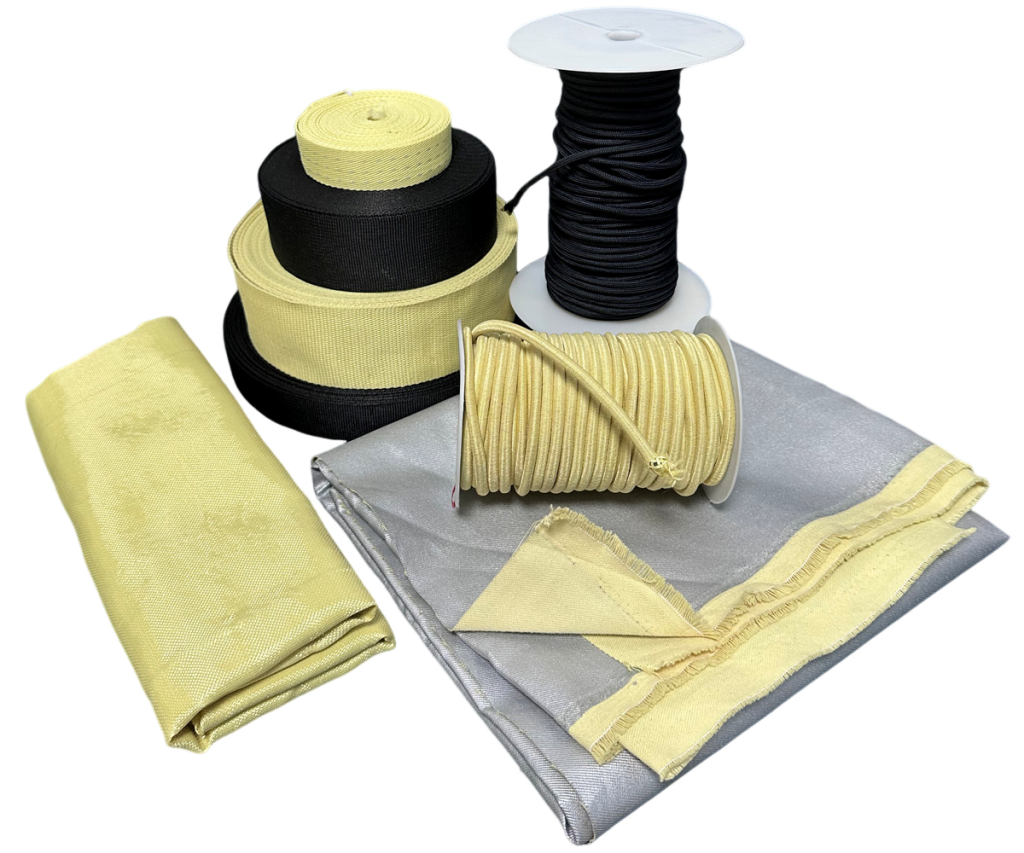
The Marvel of Aramid Fibers: Unveiling the Strength of Modern Textiles
In the world of advanced materials, aramid fibers stand out as a remarkable innovation, revolutionizing industries with their exceptional properties. Known for their high strength, heat resistance, and durability, aramid fibers have become indispensable in various applications, from protective gear to aerospace engineering. This blog delves into the fascinating world of aramid fabrics, exploring their unique characteristics, manufacturing process, and diverse uses.
What are Aramid Fibers?
Aramid fibers are a class of heat-resistant and strong synthetic fibers. The name “aramid” is derived from “aromatic polyamide,” which refers to the chemical structure of these fibers. The most well-known aramid fibers are Kevlar and Nomex, both developed by DuPont. These fibers are characterized by their high tensile strength, resistance to abrasion, and ability to withstand high temperatures without degrading.
Key Properties of Aramid Fabrics
- High Tensile Strength: Aramid fibers are incredibly strong, often compared to steel in terms of tensile strength. This makes them ideal for applications requiring durability and resistance to impact.
- Heat Resistance: Aramid fabrics can withstand extreme temperatures, making them suitable for use in environments where heat is a significant factor. They do not melt or easily ignite, providing excellent protection against fire.
- Lightweight: Despite their strength, aramid fibers are lightweight, which is a critical advantage in industries like aerospace and automotive, where weight reduction is essential.
- Chemical Resistance: Aramid fibers are resistant to many chemicals, enhancing their durability in harsh environments.
- Flexibility: These fibers are flexible, allowing them to be woven into various fabric forms, from tight weaves for protective clothing to looser weaves for filtration applications.
Manufacturing Process
The production of aramid fibers involves several sophisticated steps:
- Polymerization: The process begins with the polymerization of aromatic polyamide monomers. This creates a polymer solution that is then spun into fibers.
- Spinning: The polymer solution is extruded through spinnerets to form fibers. These fibers are then drawn to align the polymer chains, enhancing their strength.
- Heat Treatment: The fibers undergo heat treatment to further improve their mechanical properties and stability.
- Weaving: The fibers are woven into fabrics, which can be tailored to specific applications based on the desired properties.
Applications of Aramid Fabrics
- Protective Gear: Aramid fabrics are widely used in the production of bulletproof vests, helmets, and other protective clothing. Their high strength and impact resistance make them ideal for safeguarding against ballistic threats.
- Aerospace: In the aerospace industry, aramid fibers are used in the construction of aircraft components, such as fuselage panels and interior linings. Their lightweight and heat-resistant properties contribute to fuel efficiency and safety.
- Automotive: Aramid fabrics are employed in the automotive sector for manufacturing tires, brake pads, and clutch facings. Their durability and heat resistance enhance the performance and longevity of these components.
- Industrial Filtration: The chemical resistance and strength of aramid fibers make them suitable for use in industrial filtration systems, where they can withstand harsh chemicals and high temperatures.
- Sporting Goods: Aramid fibers are also found in sporting goods, such as tennis rackets, skis, and bicycle frames, where their strength and lightweight properties improve performance.
Aramid fabrics are available in different weaving processes such as woven fabric, knitted fabric, UD fabric, non-woven fabric, mesh fabric and so on.
Conclusion
Aramid fabrics represent a pinnacle of textile innovation, offering a combination of strength, heat resistance, and versatility that is unmatched by many other materials. As technology continues to advance, the applications of aramid fibers are likely to expand, further solidifying their role in modern industry. Whether in protective gear, aerospace, or everyday products, aramid fabrics are truly a marvel of modern engineering, providing safety and performance in equal measure.