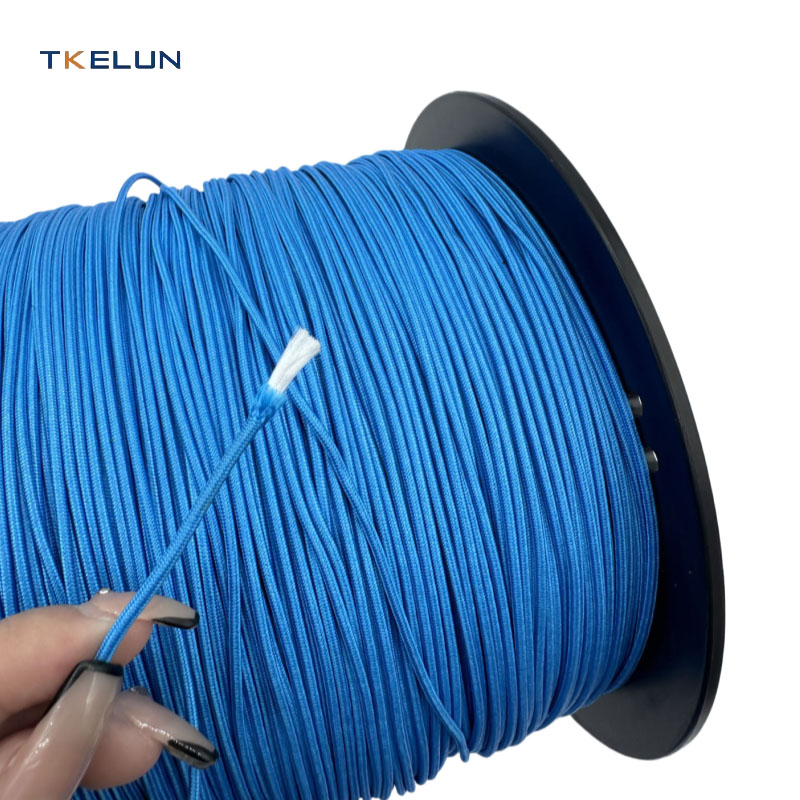
2mm UHMWPE Core Rope
50*1.3mm UHMWPE Webbing
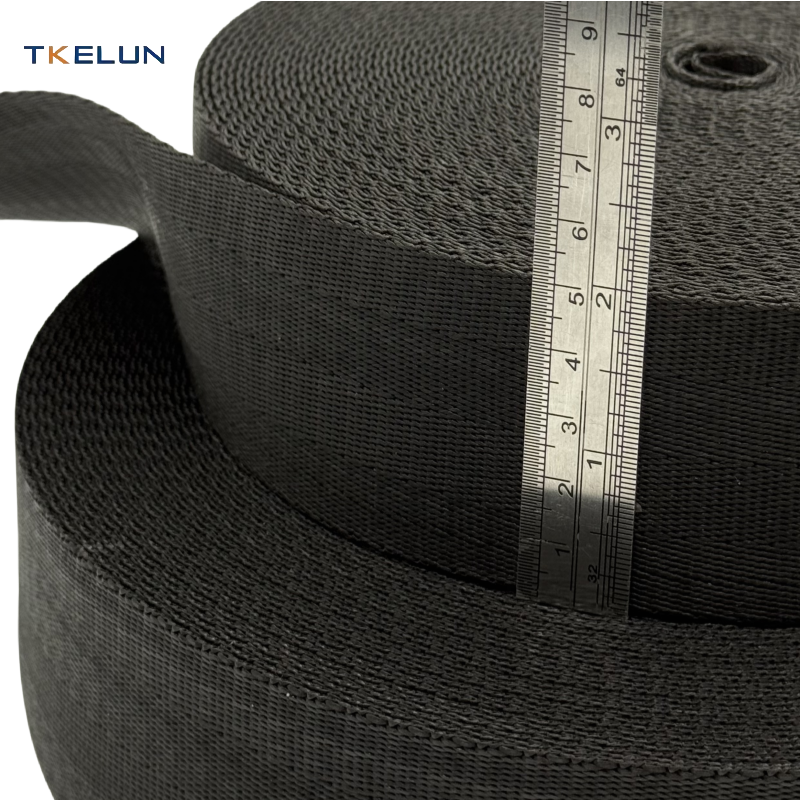
♦ Mechanical Performance
-Tensile Strength & Modulus
- UHMWPE:
The specific strength is 15 times that of high quality steel wire, 1.8 times that of carbon fiber, 1.6 times that of aramid, the tensile strength can reach more than 3.5GPa, and the modulus reaches 91-140N/tex.
- Aramid:
Strength second to UHMWPE fiber, modulus between carbon fiber and UHMWPE, typical products such as Kevlar have a strength of 3.0 GPa.
- Carbon fiber:
Highest modulus (~200-800 GPa), but slightly lower tensile strength than UHMWPE fibers.
♦ Impact Resistance & Energy Absorption
- UHMWPE:
The breaking strength is nearly twice as high as that of para-aramid, and the impact resistance is the highest among the three, making it suitable for bulletproof vests, helmets and other protective equipment.
- Aramid:
Impact resistance is moderate, but maintains good performance at high temperatures.
- Carbon fiber:
Brittle, poor impact resistance, need to be compounded with resin to enhance toughne.
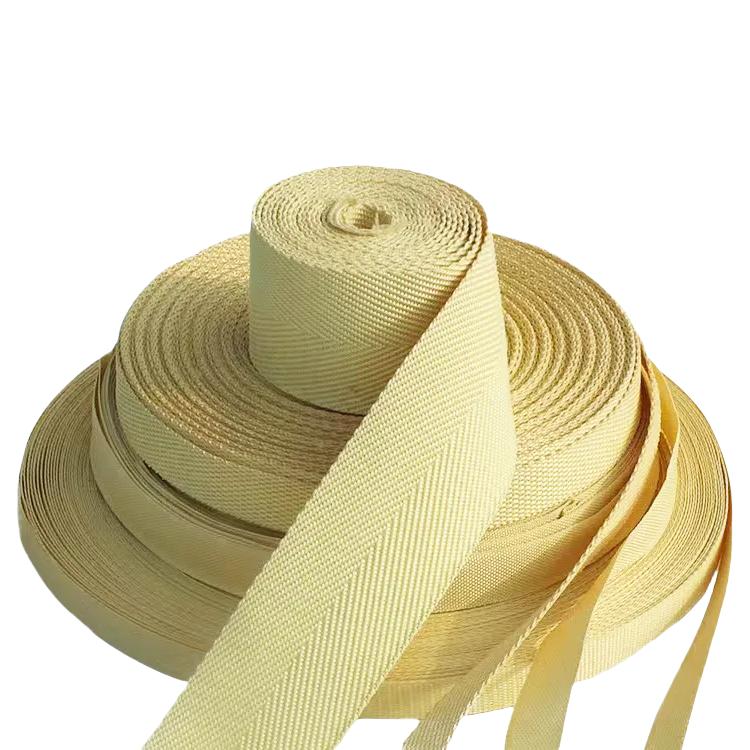
Aramid webbing
Customizable width and thickness
35*1.6mm Aramid Sleeving
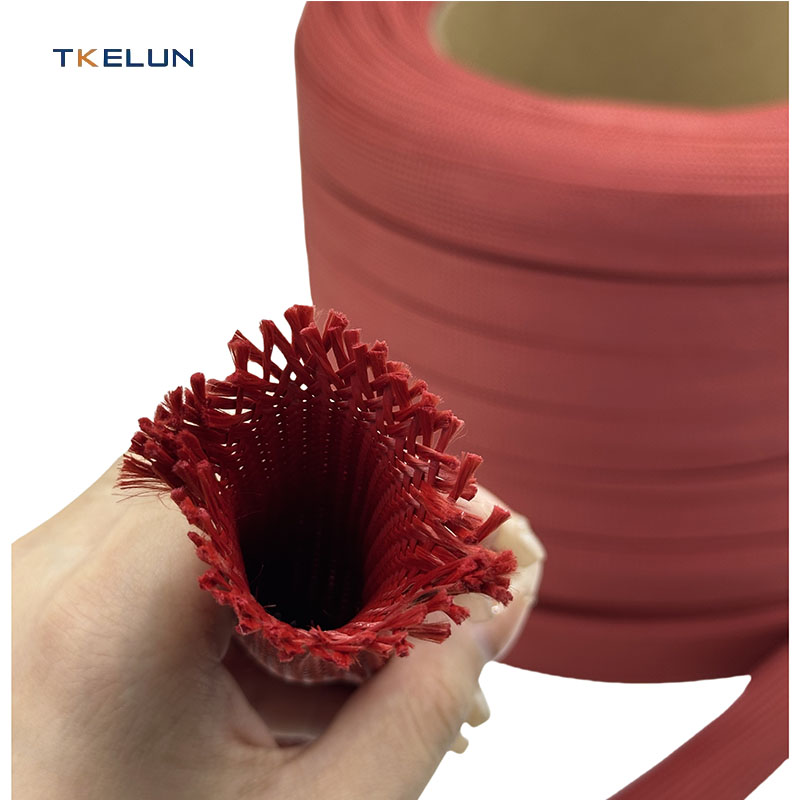
♦ Wear and fatigue resistance
- UHMWPE:
Abrasion resistance is 8 times that of carbon steel and 4 times that of nylon, and bending fatigue life far exceeds that of aramid and carbon fiber.
- Aramid:
Average abrasion resistance, prone to fiber delamination due to friction.
- Carbon fiber:
High hardness but poor abrasion resistance, requires surface coating for protection.
♦ Density & Lightweighting
- UHMWPE:
The density is only 0.97-0.98g/cm³, can float in the water, and the specific strength is 2.6 times of carbon fiber.
- Aramid:
Density 1.44g/cm³, in between.
- Carbon fiber:
Density of about 1.75-2.0g/cm³, lightweight advantage is significant but not as good as UHMWPE.
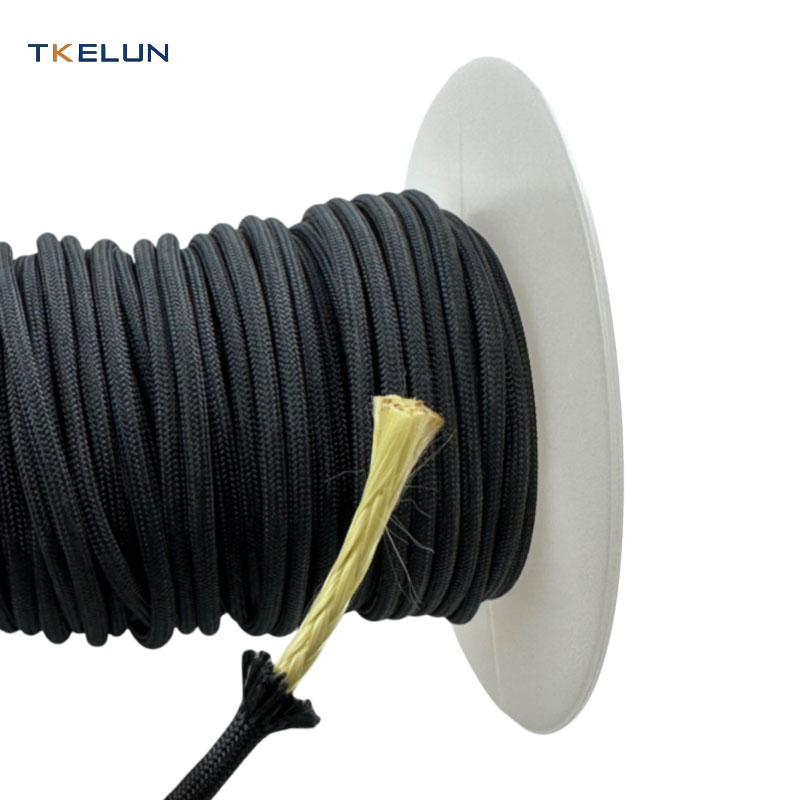
4mm Aramid Core Rope
Aramid Safety Rope
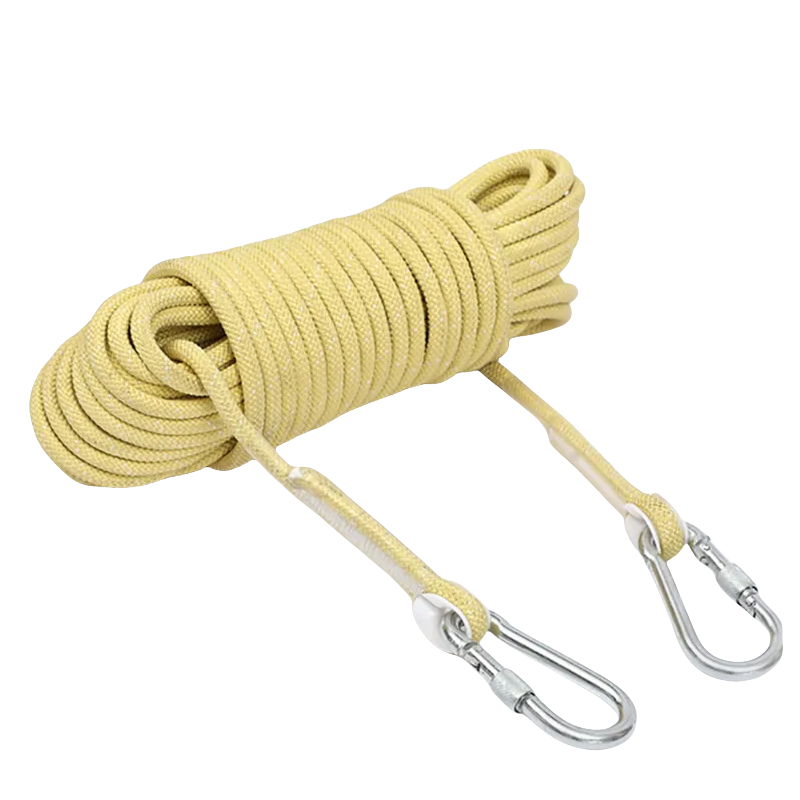
♦ Temperature Resistance
- UHMWPE:
Outstanding low-temperature resistance (-140°C to 80°C), but softens easily at high temperatures.
- Aramid:
Optimal high temperature resistance (continuous use temperature up to 200℃ or more), does not decompose at 560℃.
- Carbon fiber:
Resistant to high temperatures up to 2000°C or more (in inert environments), but deteriorates easily in oxidizing environments.
♦ Chemical Stability
- UHMWPE:
Resistant to acids, alkalis, salts and organic solvents, with excellent chemical stability.
- Aramid:
Resistant to most chemical corrosion, but easily hydrolyzed under strong acid and alkali environment.
- Carbon fiber:
Highly resistant to corrosion, but susceptible to erosion in oxidizing environments.
♦ Differences in application areas
- UHMWPE:
Bulletproof protection:
Bulletproof vests, helmets (3.6 times more effective than aramid).
Industrial & Marine:
Deep-sea mooring cables, heavy-duty slings (6,000-ton single load).
Civil Sector:
Lightweight scenarios such as climbing ropes and medical sutures.
- Aramid:
High temperature protection:
Firefighting clothing, high temperature filtration materials.
Tire reinforcement:
Tire cord fabric (to enhance abrasion resistance and safety)
- Carbon fiber:
Aerospace:
Aircraft structural parts, satellite components (30%-50% weight reduction).
New Energy:
Automotive lightweighting, battery case enhancement.
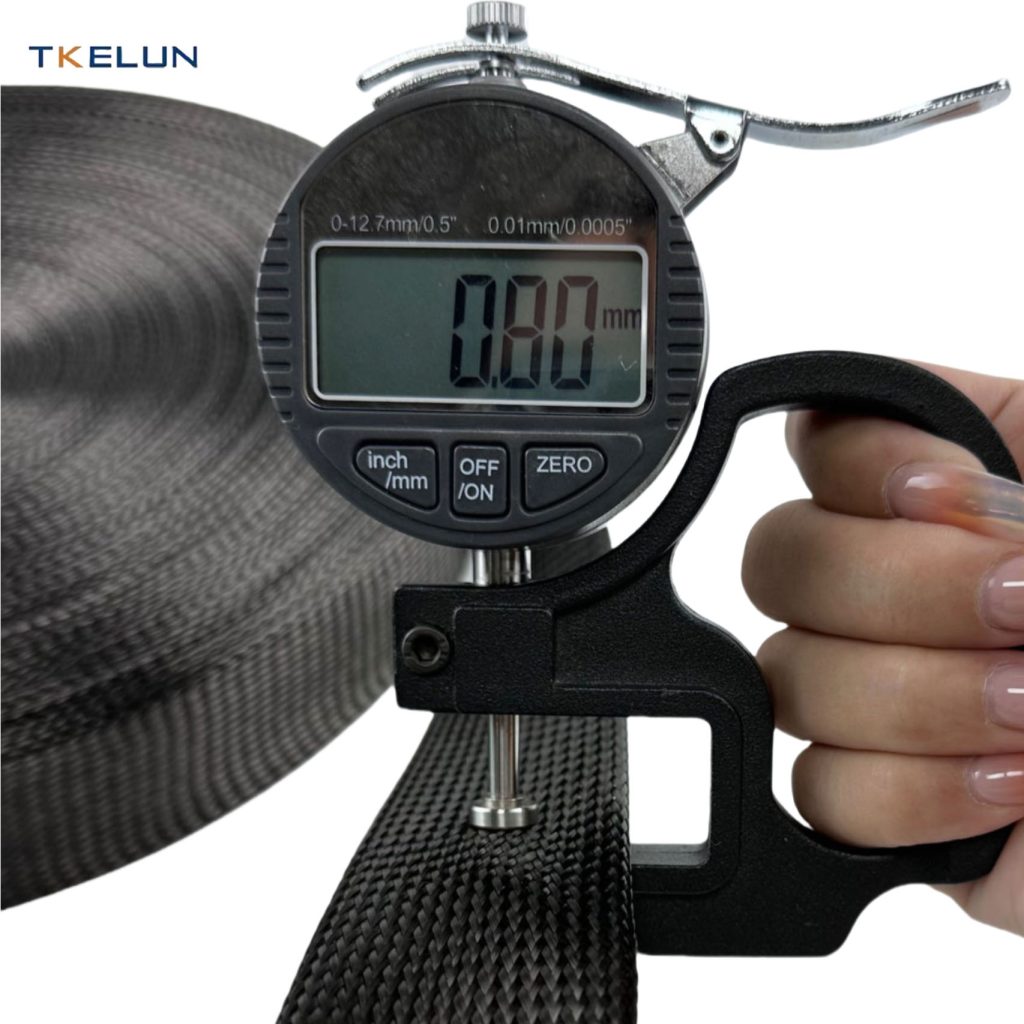
50*0.8mm Carbon Fiber Sleeve
Summary:
- UHMWPE fiber dominates in the field of protection and lightweighting with the core advantage of “light weight and high strength, abrasion and impact resistance”;
- Aramid fiber has outstanding high-temperature resistance and is suitable for extreme environments;
- Carbon fiber is used in aerospace and other high-precision fields for its high modulus and high-temperature stability.
Last!!
We accept customized the materials, width, thickness,color and length. For more technical information, please contact me.
Contact: Zoey Yuan
- Email: tksales003@tkelun.com
- Whatsapp/Wechat/Tel :+86 13267352530